Managing a hospital supply chain can be challenging in and of itself. Add supply chain disruptions to the mix and challenging becomes seemingly impossible. Fortunately, with good preparation, supply chain disruptions can be minimized, and hospitals can ensure they continue to have access to critical health and safety supplies during times of need.
Types of Disasters That Could Potentially Affect Healthcare Facility Supply Chains
While a wide variety of issues can cause a disruption of the supply chain—such as a sudden influx of appendectomies or a shortage of blood donors—there are some disasters that almost always wreak havoc on a supply chain.
Hurricanes
While hurricanes can create a number of problems for hospitals in the path of the storm, even hospitals outside the storm can be affected by these natural disasters. Case in point, when Hurricane Maria destroyed Puerto Rico – the home of many manufacturers for American medical supplies – hospitals suffered a shortage of IV saline bags. The disaster created an unprecedented shortage of this critical yet basic staple of healthcare, as the majority of hospital patients are given a saline IV.
Flu Season
The flu can wreak havoc on a hospital's supply chain. If a hospital or other healthcare facility is ill-prepared for the influx of numerous adults and children with type A or type B flu, a shortage of supplies may result. Stores of IV saline, flu shots, and Tamiflu can be depleted quickly, leaving urgent care clinics and hospitals with very little they can do to treat patients. Since dehydration with the flu is a primary cause of complications, especially in children and older adults, a shortage of IV saline can be particularly concerning.
Mass Casualty
A mass casualty is partially defined as an event that exceeds the resources typically available from healthcare facilities. Although mass casualties cannot be anticipated, they can quickly deplete a number of safety supplies, including IV saline, IV pain medications, donated blood, and other triage supplies.
A Four-Step Plan for Disasters
It's important to take steps to ensure access to health and safety supplies in the event of an emergency or natural disaster before the disaster occurs. Facilities that don't anticipate coming disasters and take action while they can are often left in a difficult situation when disaster does strike. Here's a four-step plan for disaster preparedness.
1. Plan it Out
Develop a strategy for continuing supply chain services based on emergencies. Do you have backup suppliers in case one of your suppliers experiences a disaster that prevents them from shipping your normal supplies to you? Anticipate and plan for emergencies that could happen directly to your facility as well as emergencies that could happen to other facilities that would directly impact your supply chain.
2. Communicate with Your Team
Gather a team together for the sole purpose of handling emergencies. Plan how you will work with others during an emergency situation, such as FEMA and the CDC. It takes more people to facilitate a supply chain during emergencies, so be prepared with enough staff to handle things. This may mean that some key staff members who don't ordinarily work with the supply chain receive additional training, so they can help during a disaster.
3. Identify Facilities You Will Use and Anticipate Possible Conflicts
Write out a plan for what facilities you will use in the event that your hospital or one of your suppliers is involved in a disaster. Try to visualize potential conflicts with these new facilities and find ways to circumvent them. This may require some intense forethought, but it's better to anticipate conflicts that never happen than to be faced with a conflict you never anticipated.
4. Conceptualize Your Framework
Put together a formal plan that outlines the steps your facility will take in the event of a disaster. It's critical to have everything written out in a format that can be referred back to as necessary. Make sure key people receive copies of the printed plan and keep them in an easily accessible spot. Consider what training or education needs to be provided to members of your team or anyone that will be responsible for certain tasks during an emergency. Provide that training and education to your team members well in advance and consider having a quarterly or bi-annually refresher to go over your plan and any educational initiatives to ensure everyone is on the same page.
By undergoing a bit of preparation in advance, you can be better equipped to manage your facility's supply chain to ensure continued access to safety supplies in the event of an emergency or natural disaster.

About Michael Wilson
Michael Wilson is AFFLINK'S Vice President of Marketing and Communications. He has been with the organization since 2005 and provides strategic leadership for the entire supply chain team. In his free time, Michael enjoys working with the Wounded Warrior Project, fishing, and improving his cooking skills.
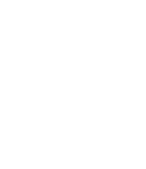