You’ve probably read it all and received tons of unsolicited advice on optimizing your warehouse inventory management practices, but following the rules doesn’t always cut it. Despite using so-called industry “best practices,” you might still be trying to clean things up and streamline processes; meanwhile, your team scrambles to locate inventory in a chaotic warehouse that the rats left to find greener pastures.
Instead of wishing you could join them, it’s time to focus on a plan that actually works. So put down your operations manual and check out our supply chain optimization and warehouse inventory management for the real world.
1. You Can Pick Your Friends
…. but can you optimize your picking process? You have options with your picking strategy, including single order, batch, and zone picking. Just make sure your process aligns with the needs of your organization – especially with active pick zones. Warehouses often run into problems when pick zones aren’t replenished and personnel need to shuffle containers to reach the objects at the back. If your order fillers are fixing other problems, they’re not picking.
2. Establish a Warehouse within Your Warehouse
If the majority of your orders are filled by a small percentage of a product line, you might consider creating a spot for them within your warehouse. This greatly reduces travel time by your pickers and it streamlines the replenishment process. Of course, you’ll have to make sure the dedicated section is easily accessible and able to accommodate heavy traffic.
3. Engage “Intelligent” Forklifts
What R2D2 was to Luke Skywalker, intelligent forklifts can be to your supply chain and warehouse inventory management. Smart forklifts incorporate solutions that enable you to direct them to a pick location, then raise and lower the lift apparatus to load designated products. Once at the drop zone, the robot knows to lower the pallet to the proper height. Intelligent forklifts allow you to optimize workflows in the warehouse and cut down on or re-purpose manpower.
4. Watch Out For Slotting
If your warehouse looks like someone lost a game of Tetris, you probably need to work at your slotting. This is an enormous opportunity to optimize your warehouse space and use every square inch of the space, which can significantly cut down on storage costs. The “honeycomb” effect that leaves empty spaces in the middle is usually caused when your organization undergoes supply chain change; your warehouse just never got the chance to catch up: If you look at the space in terms of your existing processes, would you set things up the same? If not, it’s time for some retooling.
5. Make it Rain
When all else fails, you might need to dangle a carrot for your pickers. Incentive plans can be very effective in getting the most in terms of productivity, so long as you establish a plan that can accurately measure performance.
The most influential figures in history and today didn’t get where they were by following the rules, and creativity can be a useful asset in the most unlikely of scenarios – including supply chain optimization and warehouse inventory management. The key is to identify the roadblock, then find a way around it, over it or through it. These tactics may veer far off the path of the conventional, but “normal” doesn’t always work when you’re managing a complicated supply chain and warehousing strategy.

About Michael Wilson
Michael Wilson is AFFLINK'S Vice President of Marketing and Communications. He has been with the organization since 2005 and provides strategic leadership for the entire supply chain team. In his free time, Michael enjoys working with the Wounded Warrior Project, fishing, and improving his cooking skills.
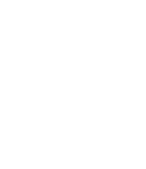