Severe weather conditions test the strength of any supply chain. Regardless of whether a forecast indicates the approach of a hurricane, a blizzard, or a prolonged heat wave, preparing for disruptions depends on careful planning and prioritization. The disruptions may occur as surges in demand for particular products, a breakdown in transportation and delivery systems, or decreased production. Here’s how to handle every disruption along the way and ensure peak supply chain optimization:
Establishing Plans A, B, and C
Part of planning involves an analysis of current supply chain strength and vulnerabilities. Supply chain strength depends on the capability to deliver products on time, and the ability to maintain profits, reputation, and competitive analysis. Vulnerabilities may include a dependency on a single supplier or system for critical goods, a gap in communications, or the lack of a disaster plan. The interdependence of a supply chain with transportation and energy systems may also exist as a vulnerability. For example, an ice storm occurring in the central United States may negatively impact travel as well as the ability of energy utilities to maintain power.
All good supply chain optimization plans should always include the personnel needed to bring the business and supply chain through a weather event.
- An emergency coordinator works with all parts of the supply chain to establish emergency planning and can serve as the primary contact.
- A business continuity manager monitors processes needed to ensure that normal operations resume and that normal transactions occur.
- Crisis management teams represent all parts of the supply chain and assist with managing recovery, restoring business operations, and communicating with emergency personnel.
Planning also considers the specific conditions that cause a supply chain to shift from normal operations to emergency procedures. Every employee throughout the supply chain should understand roles, responsibilities, and expectations when a severe weather event occurs. This should include:
- Preparedness checklist
- Watch checklist
- Active weather event checklist
- Post-weather event checklist
While a preparedness checklist covers issues such as employee training, facility maintenance, and the protection of sensitive equipment, a watch checklist signals that a forecast weather event could occur in 36 hours and ensures that usability of communications systems. Good communication allows key personnel to delegate and ensure responsibility. Communications at all levels of the supply chain cover projected downtime, service needs, and supply needs. An active weather checklist provides a 24-hour warning about possible dangerous weather conditions. After the weather event occurs, a crisis management team can use a post-weather event checklist to assess the scope and impact of interruptions to the supply chain.
When it comes to supply chain optimization, there can never be enough planning. The listed items above will work together and help to provide a seamless transition in times of weather related crisis.
Getting Extra Help Where it Matters
The application of technologies can enable preparation for hazardous weather. Supply chain management software offers features such as inventory control, warehouse management, demand planning, and capacity. Those and other features provide the technological foundation for having the right information at the right time. With many applications based in the cloud, supply chains can depend on the integrity of data used across the enterprise.
Technology solutions may also involve the use of analytics that measure the behavior of consumers before a storm event and the reliability of the supply chain before, during, and after hazardous weather. The analysis of customer preferences may allow suppliers to move inventory to key distribution points and stores. Predictive and prescriptive analytics can drive forecasting from the perspective of placing products in the needed area when demand occurs. With an emphasis on big data, supply chain firms can follow consumer demand through avenues such as social media and determine if demand exists.
Another key part of technology applications follows weather patterns and provides forecasts designed for supply chain use. Weather forecasting tools for supply chains provide an interpretation of best and worst case scenarios as well as snapshots of transportation routes, suppliers, and centers that severe weather could affect. The applications combine with supply chain management software to hold or reroute shipments and monitor warehouse status if a storm disrupts the capability of a critical supplier to deliver.

About Michael Wilson
Michael Wilson is AFFLINK'S Vice President of Marketing and Communications. He has been with the organization since 2005 and provides strategic leadership for the entire supply chain team. In his free time, Michael enjoys working with the Wounded Warrior Project, fishing, and improving his cooking skills.
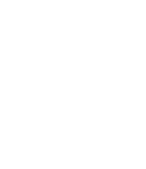