The flu has been spreading across the country with a vengeance this year, and the flu season isn’t over yet. In the U.S., flu activity typically peaks between December and February, and new cases may continue through May. And, with the CDC reporting a recent uptick in flu activity, small and large business alike are right to be fearful of the implications the virus can have on the office. Having even just a handful of employees gone for a week at a time can hurt internal and external business processes. This is a good time for facility managers to review their role in flu prevention and to catch up with current best practices.
Why are Facility Managers and Janitorial Workers on the Front Lines of Flu Prevention?
The typical seasonal flu strains that we see every year don’t spread very well by air. But that doesn’t mean that a cough or sneeze can’t make other people sick; it simply means that there’s another step in the process. When someone who’s sick with the flu coughs or sneezes, particles containing the virus settle onto the nearest surface. When the next person comes along and touches that surface, virus particles attach to their hand – and from the hand to the mouth or nose. Likewise, if sick people have virus particles on their hands, they can transfer them to anything – or anyone – they touch.
One reason the flu is so contagious is because those virus particles can live a long time away from a human host. Influenza A virus particles, for example, can survive for up to 48 hours on nonporous surfaces (doorknobs, water fountain handles, keyboards, phone receivers, file cabinets) – and up to 72 hours if the surface is wet or damp. That’s why the janitorial staff is so important during flu season. To slow down flu transmission, those surfaces have to be cleaned and disinfected both more frequently and more thoroughly than during normal daily operations.
What Steps Should Your Plan Include?
Preventing the spread of the flu is a process, not a one-time activity. The most effective strategies include these steps:
1. Identify High-Risk Areas
Start by walking through your facility and identifying high-contact surfaces. Some things – door handles, for example – are obvious. For clues to the not-so-obvious ones – just stand back and watch for a few minutes. How do people move through the workspace? And what do they touch as they do so? What areas are considered team environments? Or are there activities or habits that everyone in the office engage in, like that afternoon M&M jar?
2. Select the Right Janitorial Supplies or the Job
First, it’s important to remember that cleaning and disinfecting are not the same thing. Disinfectants lose their effectiveness when you apply them to a dirty surface. To make sure you’re really accomplishing your task, either clean first, then apply disinfectant, or choose a product that’s designed to do both. There are other factors to consider, as well:
- Efficacy: How well does the product work for what you’re trying to do? You can usually find that information on the product label. If not, either look it up online or ask your supplier.
- Contact Time: How long does the product have to be in contact with the surface you’re cleaning, and how will that affect worker productivity? Is there something else janitorial workers can do while they’re waiting the required amount of time?
- Safety: Employee safety is paramount, of course. The product’s MSDS sheet can tell you whether janitorial workers need to take any extra precautions. But it’s also important to make sure the product is intended for the surface you’ll be using it on.
- Environmental Impact: If sustainability is a priority for your company, make sure you understand the environmental impact of your janitorial supplies. Most disinfectants are registered with the EPA, which should make it easier to find out what you need to know.
3. Best Practices for flu Prevention
Cleaning during a flu outbreak is a bit different from your normal routine. Here’s what you need to know:
- Break the building into zones, with one or more teams assigned to each zone. Stress the importance of tracking which surfaces have been cleaned so that none fall through the cracks.
- If possible, put the cleaners and/or disinfectants in spray bottles rather than buckets. Repeatedly dipping janitorial supplies into the same bucket raises the risk of cross-contamination.
- Work from top to bottom, and from left to right.
- Make sure janitorial workers let the product remain in contact with the surface for the recommended period of time. Time can vary from product to product.
- Afterward, either put the used towels and other janitorial supplies in a bag for washing or, if they’re disposable, throw them away.
Other than management insisting that employees stay home when they’re sick, facility management and janitorial workers hold the key to stopping the spread of the flu. And don’t assume that we’re in the clear just because it’s almost February. An office-wide flue can happen in a matter of days. Prepare by making sure you have enough janitorial supplies on hand, educating your employees on your flu-prevention game plan, and may the odds be ever in your favor!

About Michael Wilson
Michael Wilson is AFFLINK'S Vice President of Marketing and Communications. He has been with the organization since 2005 and provides strategic leadership for the entire supply chain team. In his free time, Michael enjoys working with the Wounded Warrior Project, fishing, and improving his cooking skills.
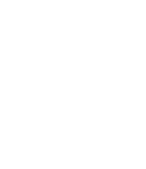