Robotic technology has been a vital segment of the industrial supply chain for decades, though recent developments have shown that it may be further changing the landscape. The upshot is that there is more flexibility and versatility in the units themselves, enabling them to handle more advanced tasks. Your supply chain can take advantage of the opportunities offered by robotics, which means that your production process can be more finely tuned and better positioned to compete in a quickly changing environment. Improvements in several key areas have made it possible for more companies to implement robotics in their supply chain operations.
- Advances in robot choreography ensure higher efficiencies while staying within safety requirements.
Supply Chain Efficiency Benchmarks: The Key To Competitive Advantage
Developers are now able to “schedule” the movement of robots on the factory floor, enabling them to be incorporated alongside human workers without disruption in the industrial supply chain. A certain distance between workers and the machines must be allowed for obvious safety reasons, but there are efficiency motives as well. When work assignments must be finished within a certain amount of time, such as paint applications or shift-end, scheduling the choreography of robots allows for smooth operations within these constraints.
- Robots are more in tune with work flows and less intrusive.
One of the biggest challenges with robots in the past is that they would interfere with work flows. Human workers must be free to move in and out of a space without having to shut down a robotics cell. In the same vein, the previous generation of robots was often hindered in their movements because they needed to allow enough distance between the machinery and humans. New technology has enabled the installation of robots in areas that were once exclusively occupied by humans
- Cages are no longer necessary for many robots.
The advancements in robotics technology for use in industry supply chain operations also means that cages are unnecessary. Special protective barriers were once required on the factory floor to prevent the injuries that could occur if a human accidentally got too close. Without cages, the capabilities of robots are more widespread, enabling more interaction with humans to streamline the manufacturing process.
Companies are already experimenting with even more advanced functions, such as re-structuring work flows on the fly. This would be extremely useful when unexpected production levels or batch size variations hit. The cage-free environment means that work scheduling can be managed more efficiently, as there is the potential to avoid production delays and the entire process becomes more responsive to real-life scenarios.
Battling Rising Healthcare Costs with Supply Chain Strategies
- Robotics enables companies to keep up with shifts in demand.
No matter how carefully you forecast, shifts in demand can hit your production facilities and cause ripples in your entire industrial supply chain. The online sales boom and introduction of an almost infinite number of product SKUs are two trends impacting demand variations. Giving the manufacturing process robotics tools to respond to shifts in demand on the fly makes the supply chain more efficient and reactive.
Research teams are striving to perfect existing robotics technology and can envision success at various levels. One development is an algorithm that manages work scheduling. The solution has the capabilities to reconfigure a shift quickly, including both its human and robotic participants. The implications for your industry supply chain are almost endless when compared to the old ways of handling work scheduling. For example, it would take a programmer a half hour or more to re-schedule four robots tasked with 20 or so functions. With the new algorithm, it’s possible to reconfigure 10 robots to perform 500 tasks in less than 10 seconds or on demand.

About Michael Wilson
Michael Wilson is AFFLINK'S Vice President of Marketing and Communications. He has been with the organization since 2005 and provides strategic leadership for the entire supply chain team. In his free time, Michael enjoys working with the Wounded Warrior Project, fishing, and improving his cooking skills.
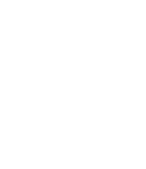