Not too long ago, we published a blog post on which metrics matter the most for supply chain optimization. If you track those metrics, you’ll have an extremely accurate portrayal of how well your supply chain is functioning. But far too many organizations make the same mistake when it comes to supply chain analysis: They do a great job of analyzing historical data, but that’s where they stop.
The supply chains that are successful going forward will be those that use predictive analysis as the foundation for making all important business decisions. Unfortunately, even forward-thinking organizations that recognize the potential of predictive analysis are making some big mistakes in execution. Here are just a few:
1. Relying on Data Scientists With Little or No Supply Chain Experience
Rumor has it that data science will be the hottest job of the next decade. Companies are understandably eager to hire the very best data scientists they can find. However, they often underestimate the importance of subject matter expertise. The value of big data can’t be overestimated; the human element will always be necessary for putting it in the right context. For example, as the number of variables in any given data stream increases so does the likelihood of false positives: the appearance of a causative relationship where none actually exists. It takes someone with deep supply chain experience to recognize those false positives and separate them from meaningful correlations.
Solution: When it comes to hiring analysts, make supply chain experience one of the top job requirements.
2. Underutilizing Real-Time Data
Supply chain analysis was designed to optimize near-real-time data. Today, however, between mobile devices and the loT, supply chains have a near-constant stream of real-time data at their fingertips. The traditional model of putting data into a batch set for overnight processing leaves valuable information sitting on the table.
Solution: Implement processes that collect and analyze data as it comes in.
3. Underutilizing Unstructured Data
Traditional analytics for supply chains were built around information that fits into neat little boxes: perfect order management, inventory days of supply, freight cost per unit, etc. In today’s world, however, the most valuable data isn’t so well behaved. Things like data from customer service phone calls, social media conversations, warranty/ return data, and customer reviews are not so easily categorized.
Solution: Develop analytics that include unstructured data to provide the most relevant insights.
4. Misidentifying Critical Predictors
In traditional supply chain analysis models, the factors given the most weight were the ones that were most obvious: like the most expensive items or the components with the highest failure rate. Predictive analytics requires the integration of “fuzzier” data, such as customer sentiment. In a nutshell, relying on the factors that were important in historical supply chain analysis can be disastrous in predictive analytics. It’s critical to correctly identify the variables that have the biggest impact on theoretical outcomes.
Solution: Don’t try to use historical models to design predictive models. Instead, identify the factors that most closely predict future events and build models around them.
Traditionally, supply chains love to look in the rearview mirror and talk about fulfillment rates, days without a lost-time accident, timeliness, and other self-bestowed accolades. And most of them are very good at it. In one survey, 73% of all respondents said they use historical data analysis for continuous improvement. But future supply chain optimization will depend on an organization’s ability to look forward, to anticipate future events and decide how those events will affect the business. For example, how will a change in fuel prices affect customer demand? What happens to your demand when a competitor runs a promotion? That future will belong to those supply chains that keep an eye on the past while focusing on what happens next.

About Michael Wilson
Michael Wilson is AFFLINK'S Vice President of Marketing and Communications. He has been with the organization since 2005 and provides strategic leadership for the entire supply chain team. In his free time, Michael enjoys working with the Wounded Warrior Project, fishing, and improving his cooking skills.
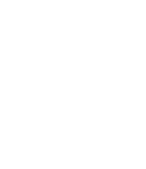