Looking to get more insight into your labor ROI and cut down on expenses? Workloading is one of the most important concepts to consider. By having an understanding of your workloading report, you will be able to gain a stronger sense of what is required from your staff and cut down on the amount of time and money that you put into the different tasks that they handle.
1. Take an Initial Audit to Understand the Processes
Before you can adjust your productivity levels and maximize your ROI, you have to understand exactly what processes need to be changed. For an easy example, let's use mopping in a commercial building. One of your tasks might be mopping the floors of employee break rooms each day. If there are two break rooms that need to be mopped and their total area is 1000 sqft, you can list "mopping the break rooms" as a separate task on your master list of all the cleaning processes that need to be completed. Once your list gets a little longer, you will want to sort it based on different types of cleaning processes or different parts of the building. Keeping a record of the different tasks and where they take place will keep you organized and allow you to see the bigger picture when it comes to facility maintenance and upkeep.
2. Determine Areas That Aren't Providing an Efficient ROI
The next step is to identify where your efforts might be falling short of optimal performance. If there is a certain area in which your facility maintenance tasks aren’t being performed properly, you must make sure to delve deeply into the process to understand why. To do this, you should take a broad view of the entire process and notice the areas that lag behind in production. For example, if you are running a janitorial staff and want to analyze their productivity levels as well as what areas of the facility are taking too long to clean, you will want to have standards in place that can measure and eliminate time from unproductive tasks.
Cleaning & Maintenance Management suggests you calculate labor hours to determine ROI by dividing the task production rate by the amount to be done, which will leave you with the task time. To apply this formula to our example above, imagine that your cleaning staff is able to effectively mop 500 sqft of break room floor per hour. Since we've got 1000 sqft of break rooms to mop, the task time is two hours.
3. Understand Time vs. Investment
Once you have been able to identify your task time or another similar identifying number, think about which areas you are investing the most in and whether or not that number could go down. To continue our mopping example, what would you do if you found that your task time suddenly doubled and your cleaning team was now taking four hours to mop the floors?
The best way to approach this situation is to drill down to task-level and see what is happening that has caused a change in the task time. Continuing our cleaning example, maybe your mopping equipment is breaking down and is causing your cleaning staff to take longer than usual. It could be that you have several new members on the team who aren't yet accustomed to how to mop efficiently enough to meet your old task time. Whatever the case may be, it's important that you try to correct it so that you aren't investing more time or money than you should be into any one specific process. This could even mean taking the time to train new employees or purchase new equipment.
4. Use Modern Tools to Help
There are a number of software tools available to assist facility managers with their efforts in making workloading more efficient. Software tools can help you understand your average levels of productivity, where adjustments can be made, what types of equipment can make upkeep run smoother, and where you can consider making changes within your facility maintenance. A quality software tool can be a huge help for any facility or supply chain manager who wants to truly understand their workloading process and how to increase their ROI.
However you decide to approach it, it's important to get a handle on your workloading so that you can keep your facility maintenance costs down and get the most out of your current resource investments.

About Michael Wilson
Michael Wilson is AFFLINK'S Vice President of Marketing and Communications. He has been with the organization since 2005 and provides strategic leadership for the entire supply chain team. In his free time, Michael enjoys working with the Wounded Warrior Project, fishing, and improving his cooking skills.
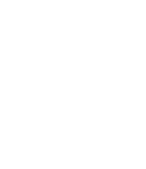