There’s a seemingly endless supply of information out there on supply chain planning, but a lot of it seems to assume you’re already an expert. But what if you’re just starting out? Or what if your business is just now at the stage where you need a comprehensive strategy rather than a “keep-doing-what-works-until-it-doesn’t” approach? If you need a crash course in Supply Chain Planning 101, we’ve got you covered.
Supply chain management is a big topic. If you’re approaching it for the first time (or if your company business is), it may help to divide your planning process into three categories: strategy, tactics, and operations.
1. Strategic Planning
Strategic planning involves big-picture, long-term decisions. Strategic supply chain planning asks the over-arching questions like, “Where are we going? Why? And how are we going to get there?” At its most basic level, the strategic stuff is why everyone in the supply chain shows up every day. Some of the decisions made at the strategic level include:
- Where will you locate your facilities, and why? What will each facility do, and why?
- Will you perform all functions in-house, or will you outsource some of them? If so, which ones?
- Who will be your supply chain partners: vendors, transporters, logistic handlers, consolidators, importers and exporters, etc.? What will your criteria be? Which things will be deal-breakers, and which are negotiable?
- What are your customers’ long-term goals? What will they need in the future, and how will you deliver it?
- What will your priorities be throughout your supply chain? Cost management? Inventory levels? On-time deliveries?
- Where will you invest your resources, and why?
- Which metrics will you use to determine success? Why?
2. Tactical Planning
This level is where you plan the how of the whats you identified at the strategic level. Now that you know where you’re going, how are you going to get there? Decisions made at this level include:
- Hammering out the contracts with your supply chain partners
- Determining capacity needs and production schedules
- Establishing quality, safety, compliance, and sustainability guidelines
- Making decisions about things like contingency planning, technology solutions, labor practices, etc.
- Evaluating the efficacy of things like drop shipments and direct store delivery
- Establishing goals/standards for the metrics by which you’ll measure success
- Deciding which, if any, technology to invest in
3. Operational Planning
The operational level focuses on how you’re going to perform the strategies and tactics determined in the other levels. It’s the level where you get down to the nitty-gritty details. It’s the level where the actual work gets done every day. Smaller businesses can sometimes get away with jumping straight to the operational level, but neglecting the strategic and tactical levels can be catastrophic for larger, more complex models. Operational planning functions include:
- Forecasting (daily, weekly, etc.)
- Scheduling (of both processes and labor)
- Reporting structures
- Oversight of vendor contract compliance
- Resolving disputes with vendors, logistics providers, transportation partners, etc.
- Managing functions like receiving, shipping, inventory control, and returns
- Determining the processes for gathering and evaluating the data used for measurement
There’s always more to learn when it comes to supply chain planning. Benchmarks and metrics move all the time, and, when they do, new best practices set the groundwork for how to get there. New technologies make things possible that were just wishful thinking six months ago. Regulatory requirements change. Supply chain partners go out of business, and new ones enter the arena. Your organization’s goals change and your supply chain has to change with them. Even the most experienced supply chain professionals aren’t shielded from the barrage of constant change. What enables them to adapt – and what will enable you to adapt – is a thorough understanding of the fundamentals of supply chain planning. In other words, strategies, tactics, and operations.

About Michael Wilson
Michael Wilson is AFFLINK'S Vice President of Marketing and Communications. He has been with the organization since 2005 and provides strategic leadership for the entire supply chain team. In his free time, Michael enjoys working with the Wounded Warrior Project, fishing, and improving his cooking skills.
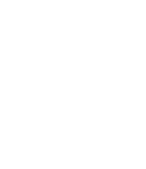